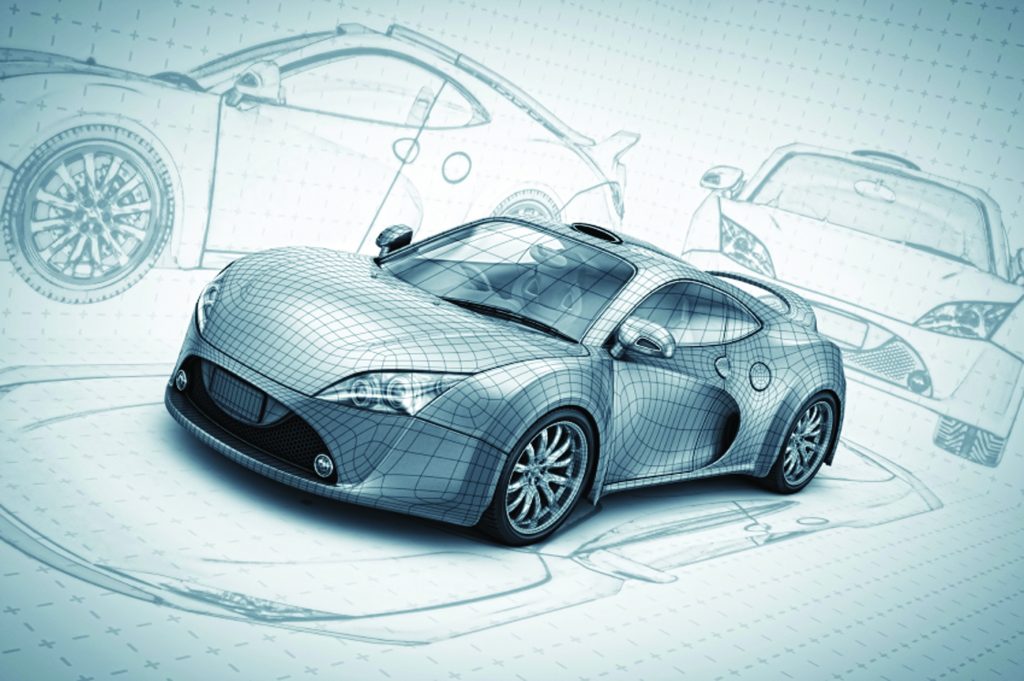
Creating an ideal 3D printable model can be intimidating to new users. If you follow this blog closely, you’ve probably heard us advise you about avoiding common 3D modeling errors. That’s why many people ask us: what happens if I place an order, but my file still contains errors?
There are clear rules for the use of each and every 3D printing material. We summarize them in something we call ‘design guides’. Sticking to the guidelines and rules in these guides will ensure that your model will be printable. That’s why we ask all designers to take a look at the design guide of their material of choice before ordering their print.
But of course, in practice it isn’t often as easy, and modeling errors can and will occur. That’s why we’ve installed a system to spot most of these mistakes. Not only does this allow us to identify unprintable files, but we will also give you feedback on what went wrong. In some case we might even be able to fix the errors on the spot!
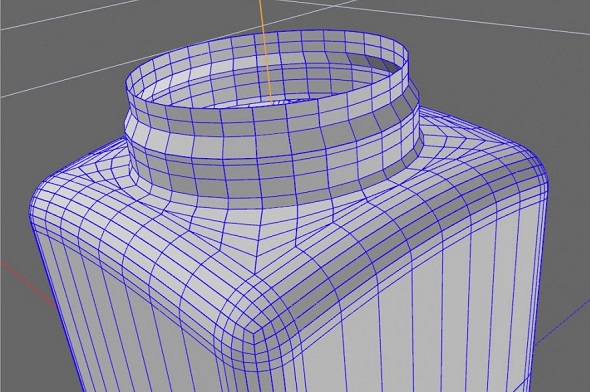
This 3D model doesn’t feature wall thickness and wouldn’t be printable.
File Repair and Consultation on Modeling Issues
So here’s how our error-spotting and file-fixing system works:
We will try to fix minor errors automatically: If you upload your model to our website and it contains errors, our software will try to fix it on the spot.
If an auto-fix doesn’t solve the error, we’ll take a look at your design in person: Our team of support engineers with years of experience in 3D modeling and 3D printing will take a look at your design. They will then give you feedback on what went wrong. Maybe the wall thickness you chose was too thin, maybe the details were too small, maybe you uploaded several models in one file. The list of possible errors might be long, but with the information that you will get from our support team, you will be able to perfect your design and make it error-free.
So as you can see, there is a safety net in place. Just a word of caution, however: As a designer it is your responsibility that your design is printable. Our software and trained personnel will do their best to spot and fix any errors, but we cannot guarantee that some errors might still slip through. That’s why it is so important to read the design guidelines before you place an order (I know I’m repeating myself, but I can’t stress enough how important they are).
Your order was cancelled? What now?
If we spot mistakes we will cancel your order and refund you completely: Whenever we find mistakes that make your model unprintable, we will cancel the order, send you an email with detailed feedback, and refund 100% of your money.
Sometimes users are surprised that their order was cancelled, even though our online tool showed them a price and they were able to place an order. That’s because receiving a quote is not a guarantee that the file is actually 3D printable.
With the instructions in the cancellation email, you will be able to fix your file and place a new order.
What can you do to make sure that your model is printable?
In order to avoid receiving the unpleasant surprise of a cancelled order, you should take a look at the three magic topics that are responsible for most design errors: minimum wall thickness, grouped models, and minimum detail size.
- Minimum wall thickness: It’s very important that every surface of your 3D model has been assigned a wall thickness. The exact minimum thickness differs from material to material. You can find a good overview and explanation here.
- Grouped models: Grouped models are two or more models that are saved within one 3D file. Although there is nothing wrong with having more than one model in a file while designing, we cannot use these designs for 3D printing. You can learn why this is the case here.
- Minimum detail size: In order to be able to print small decorative parts of your design or embossed and engraved text, these details require a specific size to be visible. This minimum detail size also differs from material to material. Find the exact values as well as further modeling rules in the design guides for each material we print.